CO₂ Laser Markers: technology, operation, and benefits for Industry
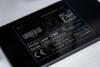
The CO₂ laser marker is a highly technological and reliable tool used for laser marking on non-metallic materials.
What is a CO₂ Laser Marker and how does It work
The CO₂ laser marker is a highly technological and reliable tool used for laser marking on non-metallic materials. This technology is based on a tube containing a gas mixture—carbon dioxide, nitrogen, helium, and in some cases hydrogen or xenon—which, when crossed by an electrical discharge, generates an infrared laser beam with a wavelength of 10.6 micrometers.
Once generated, the laser beam is focused onto the surface to be marked. The localized heat modifies the surface structure of the material, creating permanent, high-resolution engravings. This capability makes the CO₂ laser for marking a precise and versatile solution, suitable for a wide range of industrial contexts.
Modern CO₂ laser marking machines are managed by advanced software, enabling real-time content customization and integration into high-speed automated production lines.
Their reliability is one of the main reasons they are widely adopted in industries where marking quality and traceability are essential.
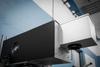
Strategic Advantages for Companies
Investing in a CO₂ laser marking system means adopting a solid, efficient, and consumable-free technology.
CO₂ laser marking is a non-contact process that does not require inks, labels, or mechanical pressure, significantly reducing operating costs and maintenance.
One of its key advantages is the engraving quality: sharp edges, crisp details, and consistent results even on curved or complex surfaces. Additionally, the system can operate continuously, ensuring high productivity even on extended shifts.
What is CO₂ Laser Used For
One of the most important aspects for companies is the compatibility with a wide range of materials, including plastic, glass, paper, wood, leather, and technical fabrics.
This makes the CO₂ laser marker an ideal solution for industries such as food packaging, cosmetics, pharmaceuticals, automotive, and industrial design.
The CO₂ laser is a gas laser that emits a beam in the infrared band, typically with a wavelength of 10.6 micrometers (μm). This characteristic makes it particularly effective for processing non-metallic materials. Power typically ranges between 10 and 400 watts, depending on the application and required productivity.
This type of laser is commonly mounted on industrial CO₂ laser markers, especially in the promotional sector, for personalizing items such as bottles, mugs, gadgets, pens, notebooks, and gift items.
Its versatility makes it the ideal choice for those seeking a flexible, fast, and adaptable marking system for a wide variety of surfaces.
Real-World Applications of CO₂ Laser Marking
CO₂ laser markers are used daily to engrave serial codes, company logos, expiration dates, traceability symbols, customized graphics, and more.
They are commonly used on:
- food packaging,
- cosmetic bottles,
- pharmaceutical blister packs,
- plastic components for electronics,
- decorative elements in wood or glass.
Thanks to their flexibility, they easily adapt to both mass production and small-scale customization needs.
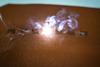
Industries Where CO₂ Laser is the Ideal Solution
- Food & beverage packaging,
- Cosmetics and personal care,
- Promotional items,
- Pharmaceutical industry,
- Electronics and technical components,
- Furniture, design, and decoration.
Why Choose a CO₂ Laser for Marking
Adopting a CO₂ laser marker means relying on a robust, efficient, and uncompromising technology. It’s a strategic choice for companies looking to:
- Optimize productivity
- Ensure quality and precision
- Reduce operating costs
- Easily integrate Industry 4.0 and traceability systems
Request a free demo or personalized consultation. The EVLaser team is available to help you identify the solution that best suits your industrial needs.
Request a Free Demo or Personalized Advice.
CO₂ Laser Marking on Various Materials
Wood
This engraving was carried out using a CO₂ laser marker, which guarantees a precise, clean, and permanent result.
The technology enables non-contact wood marking, preserving the surface and ensuring a high level of detail.
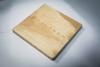
It is an ideal solution for applications in design, furniture, custom packaging, and industrial production on natural materials.
Wood is an organic material composed mainly of cellulose, hemicellulose, and lignin. The CO₂ laser, with its 10.6 μm wavelength, is well absorbed by these compounds.
On a molecular level:
- The laser energy is absorbed by organic molecules, exciting their bonds and increasing molecular vibrations.
- This vibrational energy is instantly converted into localized heat.
- The heat breaks the chemical bonds, causing pyrolysis (thermal decomposition) and carbonization.
- This results in material removal (engraving) or color variation (dark marking), along with the release of gases and organic fumes.
Result: clear engraving and surface darkening. Heat can be adjusted to achieve decorative effects or varied engraving depths.
When using a CO₂ laser marker on wood, it’s important to know that not all wood types react the same way. Though the same physical principle applies—the absorption of laser energy and its conversion into heat—wood behavior can vary significantly based on its structure, density, natural color, and resin or oil content.
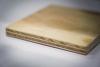
Types of Wood
Bamboo, though technically a woody grass rather than true wood, is highly suitable for laser marking. Its smooth surface and excellent absorption of infrared radiation result in well-contrasted and sharp engravings.
Beech, a light-colored wood with a fine grain, responds more delicately. Its uniform density allows for precise engravings, but its low resin content may reduce marking contrast, especially if parameters are not well calibrated. In such cases, slightly increasing the power or adjusting the speed may enhance visibility.
Cherry wood, on the other hand, offers excellent results. Its naturally warm tone and organic pigments support intense marking, with strong and uniform darkening. It is a favorite for precision or decorative work thanks to its appealing aesthetic finish.
In conclusion, knowing the characteristics of the wood you are working with is key to achieving quality laser markings. Each wood species requires specific attention and careful tuning of engraving parameters.
Black Plexiglass (PMMA – Polymethylmethacrylate)
In this application, the CO₂ laser marker engraves black plexiglass with great precision, producing a sharp and professional visual contrast.
The marking is clear, permanent, and deformation-free—ideal for technical labels, info panels, signage, and customized components in the industrial, electronics, or design sectors.
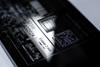
Plexiglass is a synthetic thermoplastic material that strongly absorbs CO₂ laser beams. Black plexiglass, in particular, enhances absorption of infrared radiation.
On a molecular level:
- PMMA polymer chains absorb the laser energy, causing rapid melting in the incident area.
- At higher temperatures, thermal decomposition occurs: the C-C and C-O polymer bonds break, generating monomers and volatile by-products.
- The material may partially vaporize or be removed through thermal ablation.
Result: clear marking or sharp engraving. The contrast is excellent, especially on black plexiglass, ensuring high readability. With optimized settings, flames and yellowing are avoided.
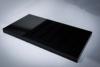
Leather
The CO₂ laser enables high-definition engraving of logos or graphics on leather, without damaging the material.
In this example, the marking is precise, uniform, and permanent—ideal for applications in the fashion, leather goods, personalized accessories, and organic material design sectors. A clean, non-contact technology, perfect for high-quality production.
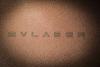
Leather, mainly composed of collagen (a protein), is a complex organic material sensitive to temperature and thermal decomposition.
On a molecular level:
- The CO₂ laser wavelengths are readily absorbed by leather, exciting the peptide bonds of proteins (amino acids).
- The energy transforms into heat, breaking molecular bonds and causing denaturation and carbonization of the proteins.
- In synthetic materials (e.g. faux leather or PU), the process involves polymer decomposition and may produce toxic fumes (hence, proper extraction is necessary).
Result: precise, dark, and permanent marking. On light leather, high contrast is achieved; on dark leather, power and frequency must be carefully adjusted to avoid damaging the material.
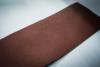