CO2 Laser Sources Types, differences and applications
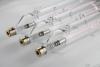
How the CO2 Laser works
Why are some lasers called CO2 lasers? Quite simply, the name refers to the creation of the laser beam by stimulating a gas mixture consisting of helium (He), nitrogen (N2), hydrogen (H2), xenon (Xe) and carbon dioxide (CO2). A CO2 laser is activated by stimulating the gas mixture with a direct current voltage (DC) or radio frequency (RF) waves. The stimulated gas mixture produces "photons" and when enough are produced, they are released by the laser as a beam. There are currently three main types of CO2 laser sources that describe how the gas mixture is retained:
- glass,
- metal,
- ceramic.
In the jargon, the term "laser source" is also commonly called laser "tube", so for example we have as sources a glass tube, a metal or ceramic tube. CO2 lasers typically emit at a wavelength of 10.6 μm, but there are dozens of other laser lines whose wavelength ranges between 9 and 11 μm (in particular at 9.6 μm).
CO2 Laser with glass source
The glass CO2 laser source is the only source stimulated by the DC voltage. The design of glass laser tubes has remained pretty much the same since their introduction in the 1960s. Currently, glass tube manufacturing is almost exclusively based in China, while most metal and ceramic tubes are manufactured in the United States. Due to the ease with which glass conducts heat along with the use of high voltage direct current to stimulate the gas mixture, all glass laser tubes must be cooled using water or a water-based coolant mixture. This continuous supply of coolant during use is very important, otherwise a glass tube could be destroyed due to the high temperatures produced by the laser. Charging the laser source with DC voltage results in a high energy consumption as glass tubes require from 15 kV (kilovolts) to 26 kV, depending on the power of the tube. A positively charged cable from the power source attaches directly to the laser tube to provide the voltage needed to activate the laser.
CO2 laser with metal and ceramic source
Metal laser tubes use a metal core / tube to hold the gas mixture instead of a glass tube, while ceramic laser tubes use a ceramic core to hold the gas. Instead of using high voltage DC, metal and ceramic laser tubes use a technique called "radio frequency" to stimulate gases to produce the beam. Using RF radio frequency has some advantages over DC voltage, including:
- lower energy consumption,
- better control of the laser engraving process,
- longer life, resulting in higher quality laser beam output for a longer period of time.
Metal and ceramic laser sources can be air or water cooled depending on the laser power.
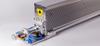
Differences between sources in glass, metal and ceramic
Now that we know how it works technically, another area to focus on is the quality of the laser beam produced. Many technical aspects contribute to the glass laser source emitting a large diameter laser beam, typically around 5mm or less depending on power and manufacturer. Also, due to the use of high voltage direct current, it is difficult to control the glass tube output in "pulsed" mode. The beam is split into small intermittent pulses of power instead of a continuous stream. It is difficult to quickly adjust the DC voltage so that pulses can be emitted. This means that a glass laser tube will not produce the best raster engraving quality, especially for engraving photographic images. It also means that marking and engraving jobs need to be done at slower speeds to get better quality.
For metal and ceramic sources that use radio frequency to generate the beam, radio waves can be turned on and off very quickly resulting in excellent pulsation, thus producing excellent engraving quality, which is very important for photographic engraving. and the precision work of the details. The metal laser source has radio frequency generating electrodes mounted inside the metal core. Ceramic sources instead have electrodes mounted outside the source due to the fact that RF can pass through the ceramic. Having electrodes outside the gas mixture can produce a better quality laser beam and less gas contamination.
The metal core of an RF laser is a metal box that is created by welding metal pieces together. Having the electrodes inside the metal core can cause chafing over time which will weaken the welds.
Degassing
As the welds weaken, outgassing from the laser source may occur. Outgassing occurs when gas “escapes” from the tube resulting in a gradual loss of laser power over time. This means that a 60-watt metal tube laser might only emit 55 watts after a few years of use. Instead, a ceramic core is created by fusing two ceramic parts together. This process produces a single, contaminant-free, solid, uniform and seamless core, eliminating the effects of outgassing. The purity of the gas directly contributes not only to the quality of the beam, but also to the life of the laser tube. The qualitative advantage of the ceramic core is the higher beam quality which results in finer details along with faster pulses, which means that highly detailed work can be processed at high speeds. There is therefore a lot of information to consider regarding the laser source, which is often referred to as the "engine" of a laser system. The choice of the best laser source depends on the final applications.
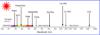
Applications of CO2 laser sources
CO2 lasers are widely used as industrial lasers for material processing, in particular for:
- cutting of plastics, wood, glass, etc., which have a high degree of absorption;
- cutting, welding and coating of metals such as stainless steel, aluminum or copper;
- laser marking of various materials;
- laser hardening, for example, of mechanical parts in steel;
- laser welding in electronics;
- 3D laser printing of polymeric materials;
- other applications include laser surgery (including ophthalmology), remote sensing (LIDAR) and spectroscopy.
If you simply want to cut out shapes of various materials, DC or RF excited sources will produce excellent quality in all cases. Regardless of the source used, the material to be cut requires more continuous energy to make its way through thick materials. If, on the other hand, we want to obtain particular details, the RF source will be able to process cuts faster than the DC excited source. Another factor to consider is power stability between sources for low power applications such as paper or thin film cutting. For DC lasers (glass tube) it is more complex to set the power below 10% of the maximum power, so you may need a lower power laser tube for sensitive applications. When cutting paper, for example, a high-powered DC laser typically causes burns due to limited power control. Power stability is greatly improved by using an RF laser source instead. In the case of applications such as continuous engraving of photos, text and logos on various materials, RF sources are clearly the best choice. Although the DC source can produce a satisfactory quality engraving, the RF source will provide both much higher engraving quality and better processing speed. If you are doing significant amounts of both engraving and cutting operations, one option may be to compare the results between both laser sources to determine what is best for your particular needs.
Duration of CO2 laser sources
The cost and investment of the laser system are also important factors to consider. The durability of the laser source plays a key role. DC laser sources are generally rated by manufacturers to last 1,000-2,000 hours (operating a 40-hour week) or approximately 1-2 years depending on the power and manufacturer of the laser source. Regarding the life span of RF sources, there is a slight difference between metal and ceramic core lasers. The metal tube RF source can last 4-6 years depending on the power and other variables, while the ceramic RF source can achieve a slightly longer life ranging from 5 to 7 years. The average cost for refurbishing or recharging the RF laser source is clearly higher than for the DC source. In summary, DC sources provide the cheapest solution for a laser on the market. However, this sacrifices processing speed and engraving quality.
The biggest sacrifice for purchasing an RF source is instead the cost of the source both initially and for refurbishing or replacing the unit. The quality of the cut will be similar to that of a DC source, but the quality of the engraving will be the best available around. The right choice is linked to weighing factors such as budget, application needs and desired final quality.
Discover below the applications and machinery for Laser Marking and Laser Welding