What can lasers do with composite fibers? Cutting, Marking and Drilling

Composites are materials created in the laboratory to obtain a product with superior properties. Most of these called "composite fibers" can be processed with the laser to perform operations such as cutting, marking and drilling.
What are Composite Fibers
Composite materials are formed by combining two or more materials with different properties to create a new material that will have properties superior to those of its individual components.Generally a fiber is added to a matrix material. An example of this is the composite of carbon fiber and epoxy resin in which the former is incorporated into the latter.
Carbon fiber is strong but not rigid enough while epoxy resin lacks strength, but the sum of these two elements produces a composite material that is both light and strong at the same time.
Another example in this sense is a composite fiber that may have the unique property of being very rigid in one direction and extremely flexible in another direction.
The main types of composite materials that can be laser processed include composites:
- fiber-reinforced polymers (FRP),
- metal matrix (MMC),
- ceramic matrix (CMC).
Lasers allow you to work with these composites and, among other things, offer an excellent option with respect to how to cut carbon fiber or cut glass fiber.
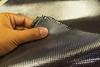
Laser processing of composite fibers
Due to their design, the structure of most composites is less uniform than elements such as plastics, metals, metal alloys and ceramics.This uneven structure makes composites more prone to damage during processing than homogeneous materials.
Delamination, fiber extraction, die chipping, heat damage and tool wear are generally major concerns when machining composites with conventional machining processes.
These challenges led manufacturers to look for ways to process composites cost-effectively without damaging them in the process, and the laser proved to be the ideal solution
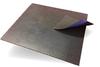
The Laser as a solution
- Nowadays, various laser sources are used for laser cutting, perforation and marking of composites, including fiber lasers, CO2 and ultrafast pulse lasers.
Each material has unique characteristics that affect the way the laser beam interacts with it and consequently the final result.
In the case of composites, the three main laser processes that can be carried out are the following:
- Laser cutting of composites. The cutting of carbon fiber or other composite materials can be carried out by setting the machinery to the appropriate wavelength. With sufficient power the laser will not only heat the material until it vaporises, but will allow you to make a clean and precise cut, leaving behind a smooth and clean edge. For organic composites, a CO2 laser with a 10.6 micron wavelength can be used, while for metal composites, laser cutting can be performed with a fiber laser with a 1 micron wavelength.
- Composite laser engraving and marking. The CO2 laser can be used to successfully remove a surface portion of composite materials thus creating a visible incision that allows you to draw patterns and images on the material or to engrave information on it.
- Laser drilling. To perform operations such as drilling, cutting and engraving, the laser power can be between 25 and 1500 watts in the case of organic matrix composites such as laminates and between 40 and 50 watts in the case of metal matrix composites. In the first case, CO2 lasers are preferred, while in the second the choice will fall on fiber lasers.
For further information read: From the C02 Laser to the Fiber Laser, we discover the most popular types of lasers
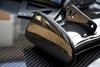
Advantages of Laser Processing of Composite Materials
- Precision of the cut. An example is the laser cutting of carbon fiber which is extremely precise and minimizes damage to the edges of the element compared to what happens with traditional mechanical cutting. Furthermore, no further processing is required once the laser cutting is completed.
- No tool wear. Traditional composite machining processes generate high tool wear and these have a very high cost. A non-contact material removal process such as laser marking is an interesting and economical alternative for some applications such as cutting and engraving.
- The material is not damaged. The processing takes place without any contact between the laser and the material and in this way any risk of damage is avoided.
- Maximum flexibility. The laser can be set up to perform various operations, such as precision laser cutting, marking and drilling. This demonstrates the extreme flexibility of this technology which can be applied to a large variety of composite fibers.
Fields of application
Lasers are a more than promising technology for the production and processing of composites in the aerospace industry, while the widespread use of advanced polymer composites in this industry is leading to their increased use in other sectors as well, particularly in the automotive industry. , where weight reduction is of increasing importance.Composites are inherently inhomogeneous, therefore, their physical properties change significantly over very small areas. In the case of carbon fiber reinforced polymer (CFRP), the most widely used composite material, the physical properties of the fiber and matrix are enormously different, as carbon fibers absorb all wavelengths of light very efficiently and they conduct heat very quickly, while the epoxy matrix absorbs and conducts much less well.
The pressure from the aerospace and transportation industry is shifting the composites industry towards the production of thermoplastic composites and the prospects in this field for lasers are even brighter, given that they are already in use for the consolidation of materials.