Why are UV lasers used: applications, characteristics and types
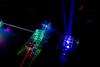
An important type of laser source used in many areas and on various materials is the Ultraviolet (UV) Laser.
The key feature of these lasers is the reduced wavelength which is between 150 and 400 nm. This characteristic makes the radiation extremely energetic and therefore allows it to interact with the chemical-physical characteristics of the materials.
What are the applications of UV lasers?
When we talk about ultraviolet light we refer to a light with a wavelength shorter than that visible to humans, since violet is the last color on the scale perceived by the human eye.UV lasers are suitable for precision applications and machining such as:
- Engraving of stamping or micro-erosion tools;
- Marking of glass and synthetic materials for which the surface is not modified in structure or chemical composition;
- Creation of small holes in the diesel injectors;
- Cleaning old paintings without affecting the original paint layers.
- Processing of overhead cables and transparent or colored pipes used in various industrial sectors;
- Precision micromachining of different materials;
- Marking of plastics for invasive medical applications and for electronic housings;
The wide range of applications of UV laser marking also includes ultrafine processing such as:
- Electronics and semiconductors,
- Plastic processing,
- Precision 3D excavation on metals,
- Processing on medical devices,
- Sensors, etc.
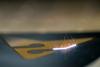
What makes Ultraviolet Lasers so suitable for these processes?
The short wavelength of ultraviolet lasers allows them to operate on tiny areas and focused spots.The short pulse widths and high energy intensities result in a small removal of material for each pulse, thus enabling the production of well-defined microstructures.
The intensity of the beam is so high that the material is removed in the vapor phase in a process called ablation, the final result of which is a clean surface.
UV laser marking is also known as cold marking because ultraviolet light breaks the bonds between the atoms and molecules of the material, preventing it from overheating, creating a thermal effect zone (HAZ) with side effects to the precision of the processing. .
The process that is generated is defined as photolytic degradation and requires minimal power to obtain clear and visible marks, since the material absorbs the light radiated by the laser to the maximum.
Discover Machines and Plants for -> Laser Marking
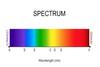
What are the types of UV lasers?
There are three main types of UV lasers.
Diode pumped solid state laser
The first is a diode-pumped solid-state laser (DPSS) Nd: YAG Q-Switch, in which duplication crystals are used to change the infrared wavelength of 1064 nm and switch it to the wavelength of the ultraviolet of 355 nm.The shape of the ray is Gaussian, so the spot will be round and with the intensity of energy gradually decreasing from the center towards the edge. The beam can be focused on spots of the order of 10 µm.
In principle, like all solid-state lasers, these ultraviolet lasers are sensitive to temperature changes.
The high repetition speed of the operation and the very small area on which they operate make these lasers the most suitable for micromachining.
Excimer laser
The second type of UV laser is a gas laser, the excimer laser. The wavelength of this laser depends on the type of gas mixture used and ranges from 180nm to over 300nm.The generated ray is not round, but has a rectangular shape with a more or less constant intensity distribution. Masks can be used to generate specific spot geometries.
Metallic vapor laser
The third type of UV laser is the metal vapor laser. The copper vapor laser is the most frequently used although vapors of many other metals can also be used.Copper vapor lasers generate radiation at a wavelength of 511 nm and 578 nm. The shape of the beam is Gaussian, which makes the laser suitable for the same range of applications as the solid-state ultraviolet laser.
Further developments of UV laser marking
UV lasers are therefore suitable for micro-scale applications with high quality results. This has opened up a wide range of applications for which only “Ultra Fast” (USP) lasers exist as an alternative technology, but with much higher costs.
The slow processing speed compared to visible and infrared laser radiation will prompt laser manufacturers to develop lasers with higher average powers and this will help reduce the cost of the technology.
With the continuous development of the laser application sector, innovation is accelerating and given the need for modern industry to perform extremely fine, fast and complex processing, an expansion of the use of this type of source is expected.
Other articles on Laser Marking -> Laser Marking of Plates and Labels for codes, texts and logos